How We Define Green
There are many definitions of “green” and “sustainable” building materials and many opinions about which chemicals to use and avoid. At Green Building Supply, we draw a hard line when it comes to hazards such as: carcinogens, formaldehyde, VOCs, pesticides, PFAS, and isocyanates. Aside from rejecting any “known” hazards, we also use the precautionary principle and avoid questionable chemicals that are potentially hazardous.
While the avoidance of hazardous chemicals is critical to one’s health, it’s only part of what makes a product green and sustainable. How a product is sourced, manufactured, and disposed of in accordance with social, economic, and environmentally-responsible methods is equally important and must be considered before we offer it.
Why Do We Research and Test?
Because our customers tell us how challenging and frustrating it is to research which products are safe and which are not. This Is due, in part, because manufacturers provide little ingredient transparency and often a lot of greenwashing. We've learned how to cut through these obstacles in order to take the worry and guesswork out of research. We've done the homework so you won't have to. After 33 years, we've learned what works, what's safe and how to solve many construction-related problems. Don't believe us? Check out our 11,000+ 5 star reviews.
What Are Our Methods?
Research
We review hundreds of eco-products and continue to test them on a regular basis. Our research begins with an in-depth study of the ingredients through Safety Data Sheets (SDS), Environmental Product Declarations (EPDs) and discussions with management, chemists and technical support professionals, reviews of third-party certifications, customer reviews, previous or pending lawsuits, and Better Business Bureau reviews, to name a few. Many of the products we test turn out not to be sustainable, don't perform very well or contain hidden toxic ingredients. We don’t sell those.
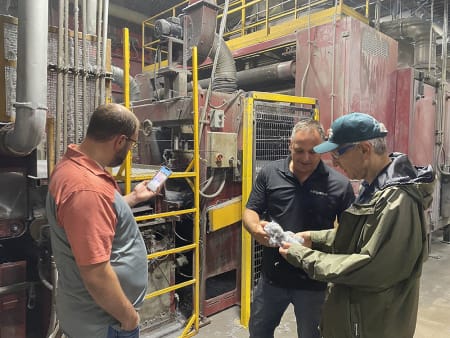
Above: Inspection of QuietWalk Plus at MP Global
We prefer to visit the factory where a product is made, if allowed, in order to personally inspect their ingredients and processes. This is one of the most transparent ways to discover the truth about a company and their products. But this is just the beginning.
Performance Testing
Every realistic approach to sustainability must require that a product last a long time and perform as good or better than its toxic counterpart. Products that don’t work well, regardless of their other benefits, won’t stand the test of time. This is why we field test all of our products to ensure that each product meets our requirements for safety and performance.
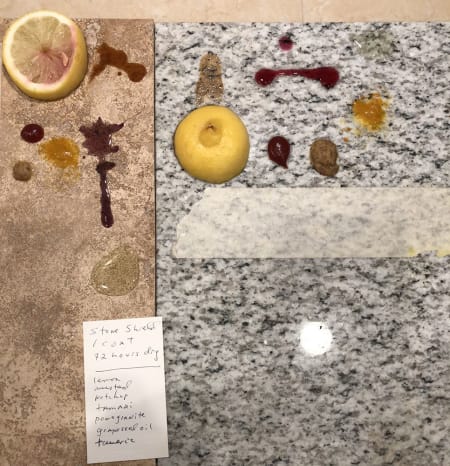
Above: Testing the effects of food on various stone sealers applied to limestone and granite
Our testing is done at our showroom facility, at our own home and at job sites in Iowa to see how products work in real life. These tests are usually done for at least a year, but are often re-tested if the manufacturer changes ingredients. Because these are live test sites indoors or outdoors, we can monitor and evaluate how they hold up to normal wear and tear over months and years.
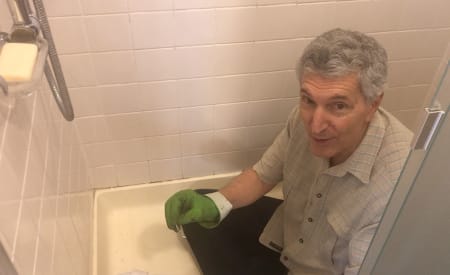
Above: Testing AFM Caulking compound in shower
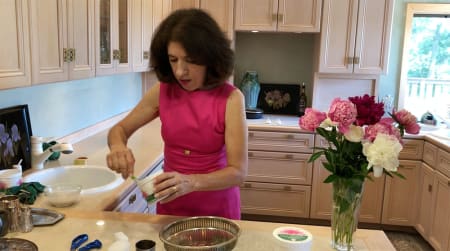
Above: Testing Blissfully Clean cleaner on silver
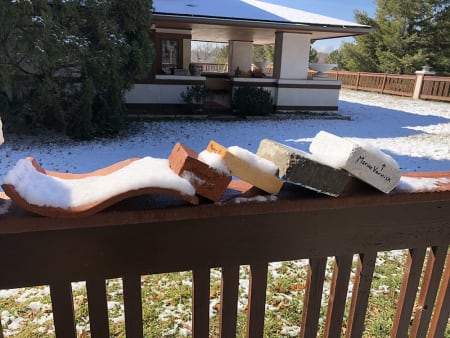
Above: Testing impact of snow, ice, sun, rain on various wood, stone, tile surfaces that have water and oil-based sealers
Personal Testing
Finally, our staff personally tests to see what impact a new product has on them physically after normal use. We do not test on animals. Some of our employees who are chemically sensitive will volunteer to test a product. Their positive or negative feedback gives us an initial indicator as to whether a product will be acceptable to others who may have a low tolerance to chemicals. While this is by no means foolproof or a triple blind study, it’s real feedback that is added to the list of criteria we use to select a product.
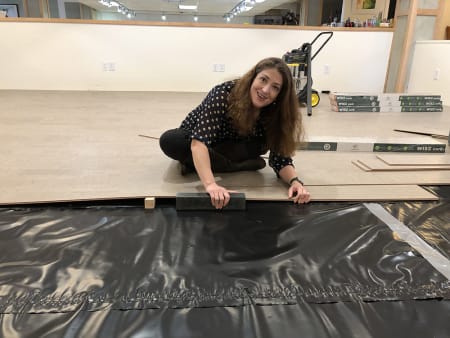
Above: Testing ease of installation of waterproof cork flooring after 10 min of training
NOTE: Even though our products have passed our tests for safety and performance and have received excellent reviews, we always recommend that you do your own test for personal sensitivity. This is a safety precaution because everyone reacts differently to a product placed in a different environment. This is especially important if you are pregnant, have allergies, asthma or sensitivities or have a history of reacting to chemicals.
We are not doctors and cannot know if you may react to our products. As a courtesy to you, Green Building Supply offers small samples of most of our products so you can test them for performance, aesthetics and your own sensitivity. This is the smart way to save time, money and avoid health issues.
Ideal Selection Criteria
Below are criteria we strive towards when we vet a product. Not every product will fulfill all of these expectations but, at a minimum, they must be safe and perform well.
They must:
- Contain no hazardous or potentially hazardous chemicals
- Have transparent ingredients ideally with a DECLARE label or EPD
- Be DIY friendly—easy to understand and apply/install
- Be independently third-party certified
- Perform as good or better than their toxic countertpart
- Be sustainable from cradle to grave with low or no carbon footprint
- Be socially, environmentally and economically responsible
- Be made from renewable resources, be recyclable and/or biodegradable, if possible
Long term research and monitoring
Once a product has been chosen, we monitor the ingredients regularly because they can change over time, especially with supply chain issues. As an example, in 2007 we offered a wonderful grout sealer that everyone loved. Then, one day, the manufacturer added Microban and never told us. Microban is made with triclosin which is a chemical with antibacterial properties. It is used in soaps, deodorants, lotions, textiles, sealers, countertops and much more. Triclosin is a known endocrine distruptor and a suspected carcinogen. It is lipophilic which means it is bioaccumlative in your body fat for long periods of time.
On Sept 9, 2016 the US Food and Drug Administration banned the incorporation of triclosan and 18 other antimicrobial chemicals from household soaps. Many countries have also banned its use. Once we discovered there was triclosin in the product, we reviewed the history and the research and discontinued the sale of the product that contained it. We even asked the company if they would make it for us without the triclosin. They declined.
Here's a better example: our QuietWalk Plus underlayment that is used beneath floating type floors was made with a different antimicrobial chemical. Fortunately the manufacturer advised us of their intentions so we asked them if they would make it for us without the antimicrobials. And they said "yes"! This made our customers very happy, and this product has now become one of our best selling products. We are the only company in the US that now offers it in this pure form. We wish every manufacturer would be as willing to make their products safer.
At Green Building Supply, we’re always looking for safer products that perform exceptionally well. If you happen to find one, please don’t hesitate to let us know. We will test it ourselves and if it meets our standards, we’ll most likely offer it to others. Most of our products were discovered this way.